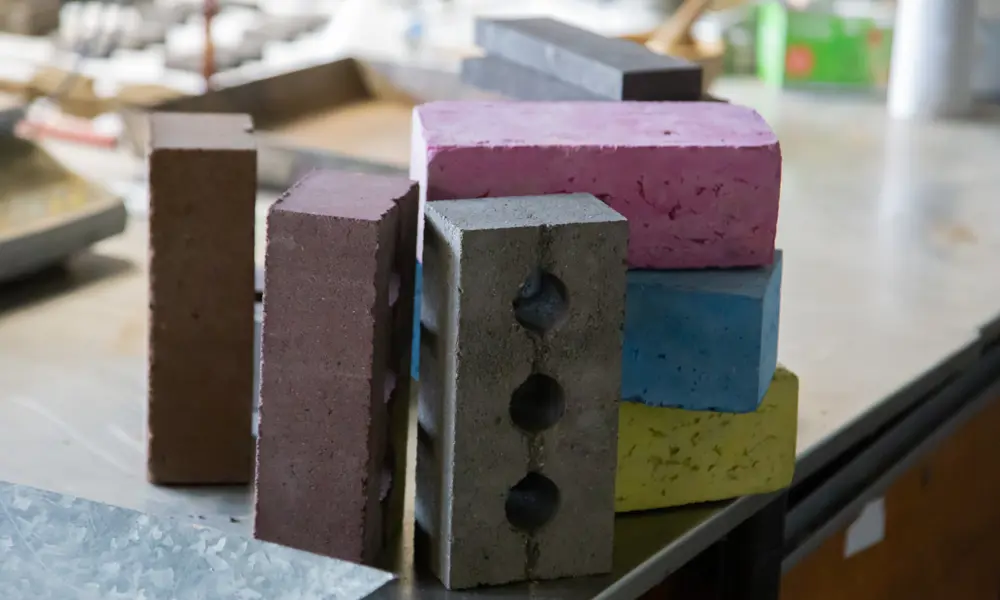
Innovation Watch - Another brick in the wall
K-briqs can be made in a range of colours by adding recycled pigments to the mix
With natural resources running low, Scottish engineers have created a brick that uses more than 90% recycled building materials.
In 2019, the UK made two billion bricks but still needed to import an additional 600 million. The UK government’s new house-building targets are increasing demand for new building materials, but many construction products are unsustainable and more than 30% of landfill waste comes from the construction and demolition of buildings.
Kenoteq, a Heriot-Watt University spinout, has used this construction and demolition waste to create a sustainable building product that is formed of over 90% recycled materials. The K-Briq looks and behaves like a clay brick and weighs the same but offers better insulation properties. The bricks don’t need to be fired, so produce just 10% of the carbon emissions that standard fired bricks create. At the end of their life, the bricks can be ground back down to create new K-Briqs, beginning the cycle again.
The company arose from a partnership between Dr Sam Chapman, a structural engineer with an interest in carbon footprinting and engineering professor Gabriela Medero. Professor Medero had been thinking about how construction materials could be reused for more than 10 years, with an aim to create a more circular economy in construction. Having just completed a PhD in carbon assessment of wind power, Dr Chapman stepped in to carry out a carbon assessment of the potential product and looked at the lifecycle carbon emissions. The pair then applied for a Royal Academy of Engineering Enterprise Fellowship with their prototype to develop and support commercialisation of the product.
Kenoteq set up its pilot production onsite with a waste handling company. Kenoteq collects inert demolition waste, for example old bricks, rubble and gypsum plaster, before mixing the waste with its binder and compressing it into bricks. Recycled pigments can also be added to produce bricks in any colour. By partnering with companies that already deal with construction waste, Kenoteq ensures that it is not adding trucks to the road – the heavy waste comes to the site anyway, and empty trucks going to collect waste from building sites are ideally suited to deposit the finished product in a place that requires it.
The regulatory process involved in bringing a new product to market is understandably extensive and challenging. The main certifying bodies have been guiding the team through the certification process, and the team has conducted extensive testing and development at Heriot-Watt University to ensure that the bricks could meet safety standards.
K-Briq modules were due to make their debut in this year’s Serpentine Pavilion – an annual architectural event. The Pavilion, designed by South African architectural studio Counterspace, is using custom-sized K-Briq modules, allowing Kenoteq to test and experiment with new colours and textures. However, due to the COVID-19 pandemic, the opening has been postponed until 2021.
By the end of the year, Kenoteq is aiming to scale-up its manufacturing capacity to three million bricks a year. It is also aiming to create a brick out of 100% recycled material, and exploring options to expand its product range to other building materials. For more information, visitwww.kenoteq.com or @Kenoteq
Keep up-to-date with Ingenia for free
SubscribeOther content from Ingenia
Quick read
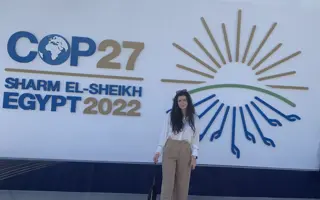
- Environment & sustainability
- Opinion
A young engineer’s perspective on the good, the bad and the ugly of COP27
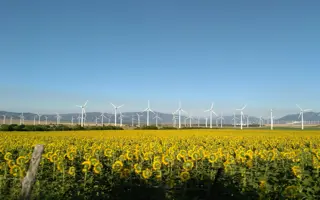
- Environment & sustainability
- Issue 95
How do we pay for net zero technologies?
Alex Keeler: Electrifying trains and STEMAZING outreach
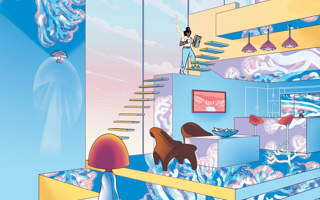
- Civil & structural
- Environment & sustainability
- Issue 95